Spanntechnik
Ab jetzt finden Sie unser Sortiment an Spanntechnikprodukten auch in unserem Onlineshop!
Dieses beinhaltet verschiedene Drehdurchführungen, Spannsätze, Löseeinheiten, Spannzangen, Einbauspannköpfe und mehr.
Ab jetzt ist unser Sortiment an Spanntechnikprodukten auch in unserem Onlineshop erhältlich!
Dort finden Sie Drehdurchführungen, Spannsätze, Löseeinheiten, Spannzangen, Einbauspannköpfe und mehr.
Startseite » Spanntechnik
Im Bereich der Zerspanung stellen Präzision, Effizienz und Prozesssicherheit die Kernanforderungen dar. Hierbei bietet die Spanntechnik als Bindeglied zwischen Maschine und Werkzeug als auch zwischen Maschinentisch und Werkstück eine optimale Voraussetzung, um den Prozess zu verbessern. Die jeweilige Fixierung der Werkzeuge und Werkstücke erfolgt dabei elektrisch, pneumatisch, hydraulisch, per Vakuum oder mechanisch von Hand. Des Weiteren gibt es in der Spanntechnik nicht das eine Spannsystem für alle Anwendungsfälle, da die Entscheidung des richtigen Spannsystems von vielen Faktoren beeinflusst wird.
Grundsätzlich unterscheidet man zwischen der Werkzeug- und Werkstück-Spanntechnik.
Werkzeug-Spanntechnik
Ein Blick auf die Entwicklung der Werkzeugspannsysteme zeigt im Wesentlichen zwei Kernaspekte: Einerseits hat die Variantenvielfalt über die Jahre stark zugenommen und andererseits gewinnen Präzisionsaufnahmen zunehmend an Bedeutung. Diese Entwicklungen lassen sich dadurch begründen, dass mit einer zunehmenden Qualität und Leistungsfähigkeit der Werkzeugmaschinen auch die Anforderungen an die Prozesssicherheit sowie an die Werkzeugstandzeiten steigen. Schnellwechselsysteme und modulare Baukasten bieten hierbei vielfältige Möglichkeiten, ein schnelles Umrüsten der Spannmittel zu ermöglichen und die Produktion flexibler zu gestalten. Durch die in den vergangenen Jahren immer weiter voranschreitende Digitalisierung in der Fertigung gewinnen Sensoren in Spannsystemen an Bedeutung. Sensoren, die direkt in das Spannsystem integriert werden, liefern während der Bearbeitung wichtige Daten und gewährleisten eine Zustandsüberwachung des Werkzeugs und des dazugehörigen Halters. Vor allem in der Massenfertigung setzen Zerspaner nach und nach auf intelligente Fertigungsstrukturen mit einem hohen Automatisierungsgrad.
Die verschiedenen Schnittstellen zur Maschine
In der Praxis werden Maschine und Spindel häufig über einen Kegelschaft verbunden. Dabei sind für die Aufnahme der Werkzeughalter in die Maschine genormte Schnittstellen unerlässlich. Diese unterscheiden sich in ihrer Automatisierbarkeit, Spannsicherheit, Wechselgenauigkeit und den optimalen Drehzahlbereichen. Die eingesetzten Werkzeughalter müssen die benötigte Bearbeitungskraft optimal von der Spindel auf das Werkzeug übertragen. Steifigkeit, Spannkraft, Schwingungsdämpfung und die Rundlaufgenauigkeit dürfen hierbei nicht vernachlässigt werden.
Folgende Schnittstellen existieren in der Werkzeug-Spanntechnik:
- Morsekegel (MK): Der Morsekegel gehört zu den ältesten Werkzeugschnittstellen und ist nach DIN 228 genormt. Meist wird diese Schnittstelle in handbetätigten Bohrmaschinen eingesetzt, wobei die Drehmomentübertragung mittels Haftreibung im Kegel erfolgt. Die MK-Schnittstelle ist selbsthemmend und daher nicht automatisierbar, da er manuell aus dem Aufnahmekonus entfernt werden muss. In Drehmaschinen und Bearbeitungszentren werden heute hauptsächlich Steilkegel und Hohlschaftkegel verwendet.
- Steilkegel (SK): Die
SK-Schnittstelle ist nach DIN 69871 und 2080 genormt. Der deutlich steilere und weit verbreitete Steilkegel ist durch seinen relativ großen Kegelwinkel nicht selbsthemmend. Er zentriert sich bei Werkzeugwechsel gut und ist leicht lösbar. Bei dieser Schnittstelle muss das Werkzeug durchgehend in die Aufnahme hineingezogen werden. Die Kraftübertragung erfolgt reibschlüssig über den Kegel. Eine sichere Drehmomentübertragung wird über Nuten gewährleistet, in die Nutensteine an der Arbeitsspindel greifen und so ein Formschluss ermöglichen. Bei hohen Drehzahlen nehmen die auftretenden Kräfte zu und bringen die SK-Schnittstelle an seine Grenzen, da Zentrifugal- bzw. Fliehkräfte die Kegelhülse der Hauptspindel aufweiten. Dadurch wird das Werkzeug im Betrieb weiter hineingezogen und verklemmt im Stillstand. Aus diesem Grund war es notwendig eine Schnittstelle zu entwickeln, die für sehr hohe Drehzahlen geeignet ist, wodurch der Hohlschaftkegel entstanden ist.
- Hohlschaftkegel (HSK): Die
HSK-Schnittstelle ist nach DIN 69893 genormt und kann als Weiterentwicklung des Steilkegels betrachtet werden. Der Hohlschaftkegel ist dabei in einem Forschungsprojekt der RWTH Aachen in enger Zusammenarbeit mit Partnern aus der Industrie entstanden. Gegenüber der SK-Schnittstelle ist der Hohlschaftkegel rund 50% leichter und 30% kleiner, was den Werkzeugwechsel nicht nur vereinfachen, sondern auch beschleunigen soll. Der kleinere Kegelwinkel sorgt dafür, dass die HSK-Schnittstelle an der Stirnfläche der Arbeitsspindel anliegt. Dies führt zu einer hohen Steifigkeit und Wechselgenauigkeit in axiale Richtung. Die Übertragung des Drehmoments erfolgt hierbei kraftschlüssig über Kegel- und Anlagenflächen sowie formschlüssig über zwei Mitnehmernuten. Der Hohlschaftkegel eignet sich besonders gut für hohe Umdrehungsfrequenzen, da die hohen Kräfte die Spannelemente nach außen drücken und die Spannkraft an der Kegelfläche verstärken.
Aufnahmen für verschiedene Werkzeuge
Am Steil- bzw. Hohlschaftkegel lassen sich Werkzeuge mit Hilfe verschiedener Aufnahmen unterschiedlich spannen. Die Werkzeuge sollten in den jeweiligen Bearbeitungszentren so gespannt sein, dass eine sehr gute Plan- und Rundlaufgenauigkeit sowie eine hohe Wiederholgenauigkeit in der Positionierung beim Werkzeugwechsel gewährleistet wird. Auch ist auf eine gute Biege- bzw. Verdrehsteifigkeit und auf die Möglichkeit hoher Umdrehungsfrequenzen zu achten. Zu den unterschiedlichen Aufnahmen zählen:
- Spannzangenfutter
- Weldon-Aufnahmen
- Bohrfutter
- Schrumpffutter
- Hydrodehnspannfutter
Werkstück-Spanntechnik
Ein schnelles und präzises Spannen von Werkstücken ist für die Leistungsfähigkeit und die Performance der Zerspanung entscheidend. Denn damit sich eine Produktion langfristig rechnet, muss das Fertigungsverfahren effizient und wirtschaftlich sein. Hierbei kann die Werkstück-Spanntechnik einen wichtigen Beitrag leisten, indem sie eine sichere Verbindung zwischen Maschinentisch und Werkstück gewährleistet.
Die verschiedenen Spannmittel
Welcher Halter für ein prozesssicheres Spannen des Werkstücks auf der Maschine am geeignetsten ist, hängt im Wesentlichen vom jeweiligen Bearbeitungsverfahren und der Form des zu bearbeitenden Bauteils ab. Im Folgenden werden die unterschiedlichen Spannmittel aufgezeigt:
- Spannfutter: Kraft- bzw. Handspannfutter werden insbesondere auf Drehmaschinen eingesetzt. Es besteht aus einem Flansch, der die Maschinenspindel mit dem Futterkörper verbindet. Dieser umschließt und stabilisiert die Spannstelle. Ein sogenannter Zugrohradapter verbindet die Spannmittelkupplung mit dem Spannzylinder der Maschine und öffnet oder schließt das Spannsystem.
Die Kupplung hält und bewegt den Spannkopf, welcher das Werkstück fixiert. Zur exakten Positionierung des Werkstücks wird ein Grundanschlag verwendet, dieser kann entfernt werden, um vollen Durchlass für die Stangenbearbeitung zu erhalten.
Die Spannfutter besitzen meist drei Spannbacken, für andere Geometrien oder dünnwandige Bauteile können auch vier, sechs oder mehr Backen verwendet werden. Die Spannbacken haben einen großen Einfluss auf die Spannqualität und die Spannsicherheit. Dabei wird zwischen harten und weichen Spannbackensätzen unterschieden. Harte Spannbacken sind verschleißfest, eignen sich für große Spannkräfte und besitzen verzahnte Spannflächen, welche allerdings die Oberfläche des Werkstücks beschädigen. Weiche Backen beschädigen die Oberfläche des Werkstücks nicht, besitzen eine hohe Wiederholspanngenauigkeit und können im Durchmesser sowie der Tiefe angepasst werden. Damit die Nutzung bei höheren Bearbeitungsdrehzahlen gewährleistet werden kann, ist das Spannfutter mit einem Fliehkraftausgleich ausgestattet. Dadurch können Spannkraftverluste ausgeglichen werden. Beim Beladen des Spannfutters wird das Werkstück in den Spannkopf geführt und durch den Grundanschlag positioniert. Der Spannkopf wird in den Konus gezogen und schließt sich um das Werkstück, wodurch dieses kraftvoll gegen den Grundanschlag gezogen wird. Die daraus resultierende steife Spannung reduziert Vibrationen während der Bearbeitung und stabilisiert das Werkstück.
- Spanndorn: Typischerweise wird der Spanndorn direkt auf einer Maschinenspindel befestigt und über eine keglige oder zylindrische Aufnahme zentriert. Somit werden beim Drehen die Drehbewegungen und -momente auf das eingespannte Werkstück weitergeleitet. Die Innenspannung erfolgt in einer Bohrung oder Innenkontur. Das haltende Element des Spanndorn ist die Segmentspannbüchse. Die Spannbüchse wird von einer Kupplung bewegt, welche wiederrum von einem Dornkörper gehalten wird, und wird von dem Spannmittel betätigt, auf dem der Spanndorn montiert ist. Die Kupplungsschale verbindet Spannbüchse und Kupplung. Auch beim Spanndorn positioniert und stabilisiert der Grundanschlag das Werkstück und schützt obendrein vor Verschmutzung im Spannsystem. Beim Beladen des Werkstücks wird die Spannbüchse auf den Konus gezogen und weitet sich, wodurch sie am gesamten Durchmesser Kontakt zum Werkstück hat und es gegen den Grundanschlag zieht. Dadurch wird das Werkstück stabilisiert und Vibrationen werden verringert.
- Spannzange: Im Gegensatz zum Spanndorn kommt die Spannzange bei der Außenspannung zum Einsatz. Sie ermöglicht ein genaues, schnelles und kraftschlüssiges Aufspannen. Die Spannzange besteht aus einer kegelförmigen radial geschlitzten Hülse mit einer runden, und manchmal auch quadratischen oder sechseckigen Bohrung. Dazu gehört eine Spannzangenaufnahme mit passendem Innenkegel. Die Spannung erfolgt mittels Überwurfmutter, mit der die Spannzange in den Innenkegel der Aufnahme gedrückt wird. Durch die Schlitzung wird die Bohrung im Spannmittel gleichmäßig zusammengedrückt, wodurch das Werkstück kraftschlüssig festgehalten wird.
Werkzeug-Spanntechnik
Ein Blick auf die Entwicklung der Werkzeugspannsysteme zeigt im Wesentlichen zwei Kernaspekte: Einerseits hat die Variantenvielfalt über die Jahre stark zugenommen und andererseits gewinnen Präzisionsaufnahmen zunehmend an Bedeutung. Diese Entwicklungen lassen sich dadurch begründen, dass mit einer zunehmenden Qualität und Leistungsfähigkeit der Werkzeugmaschinen auch die Anforderungen an die Prozesssicherheit sowie an die Werkzeugstandzeiten steigen. Schnellwechselsysteme und modulare Baukasten bieten hierbei vielfältige Möglichkeiten, ein schnelles Umrüsten der Spannmittel zu ermöglichen und die Produktion flexibler zu gestalten. Durch die in den vergangenen Jahren immer weiter voranschreitende Digitalisierung in der Fertigung gewinnen Sensoren in Spannsystem an Bedeutung. Sensoren, die direkt in das Spannsystem integriert werden, liefern während der Bearbeitung wichtige Daten und gewährleisten eine Zustandsüberwachung des Werkzeugs und des dazugehörigen Halters. Vor allem in der Massenfertigung setzen Zerspaner nach und nach auf intelligente Fertigungsstrukturen mit einem hohen Automatisierungsgrad.Die verschiedenen Schnittstellen zur Maschine
In der Praxis werden Maschine und Spindel häufig über einen Kegelschaft verbunden. Dabei sind für die Aufnahme der Werkzeughalter in die Maschine genormte Schnittstellen unerlässlich. Diese unterscheiden sich in ihrer Automatisierbarkeit, Spannsicherheit, Wechselgenauigkeit und den optimalen Drehzahlbereichen. Die eingesetzten Werkzeughalter müssen die benötigte Bearbeitungskraft optimal von der Spindel auf das Werkzeug übertragen. Steifigkeit, Spannkraft, Schwingungsdämpfung und die Rundlaufgenauigkeit dürfen hierbei nicht vernachlässigt werden. Folgende Schnittstellen existieren in der Werkzeug-Spanntechnik:- Morsekegel (MK): Der Morsekegel gehört zu den ältesten Werkzeugschnittstellen und ist nach DIN 228 genormt. Meist wird diese Schnittstelle in handbetätigten Bohrmaschinen eingesetzt, wobei die Drehmomentübertragung mittels Haftreibung im Kegel erfolgt. Die MK-Schnittstelle ist selbsthemmend und daher nicht automatisierbar, da er manuell aus dem Aufnahmekonus entfernt werden muss. In Drehmaschinen und Bearbeitungszentren werden heute hauptsächlich Steilkegel und Hohlschaftkegel verwendet.
- Steilkegel (SK): Die SK-Schnittstelle ist nach DIN 69871 und 2080 genormt. Der deutlich steilere und weit verbreitete Steilkegel ist durch seinen relativ großen Kegelwinkel nicht selbsthemmend. Er zentriert sich bei Werkzeugwechsel gut und ist leicht lösbar. Bei dieser Schnittstelle muss das Werkzeug durchgehend in die Aufnahme hineingezogen werden. Die Kraftübertragung erfolgt reibschlüssig über den Kegel. Eine sichere Drehmomentübertragung wird über Nuten gewährleistet, in die Nutensteine an der Arbeitsspindel greifen und so ein Formschluss ermöglichen. Bei hohen Drehzahlen nehmen die auftretenden Kräfte zu und bringen die SK-Schnittstelle an seine Grenzen, da Zentrifugal- bzw. Fliehkräfte die Kegelhülse der Hauptspindel aufweiten. Dadurch wird das Werkzeug im Betrieb weiter hineingezogen und verklemmt im Stillstand. Aus diesem Grund war es notwendig eine Schnittstelle zu entwickeln, die für sehr hohe Drehzahlen geeignet ist, wodurch der Hohlschaftkegel entstanden ist.
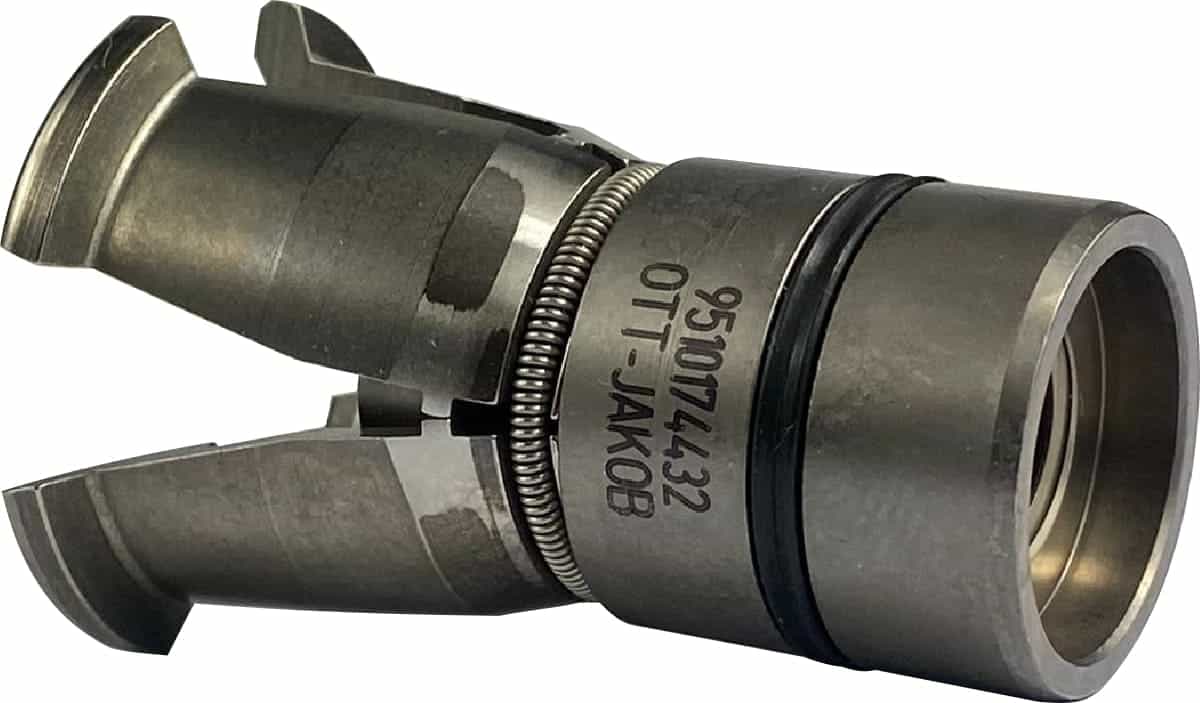
- Hohlschaftkegel (HSK): Die HSK-Schnittstelle ist nach DIN 69893 genormt und kann als Weiterentwicklung des Steilkegels betrachtet werden. Der Hohlschaftkegel ist dabei in einem Forschungsprojekt der RWTH Aachen in enger Zusammenarbeit mit Partnern aus der Industrie entstanden. Gegenüber der SK-Schnittstelle ist der Hohlschaftkegel rund 50% leichter und 30% kleiner, was den Werkzeugwechsel nicht nur vereinfachen, sondern auch beschleunigen soll. Der kleinere Kegelwinkel sorgt dafür, dass die HSK-Schnittstelle an der Stirnfläche der Arbeitsspindel anliegt. Dies führt zu einer hohen Steifigkeit und Wechselgenauigkeit in axiale Richtung. Die Übertragung des Drehmoments erfolgt hierbei kraftschlüssig über Kegel- und Anlagenflächen sowie formschlüssig über zwei Mitnehmernuten. Der Hohlschaftkegel eignet sich besonders gut für hohe Umdrehungsfrequenzen, da die hohen Kräfte die Spannelemente nach außen drücken und die Spannkraft an der Kegelfläche verstärken.
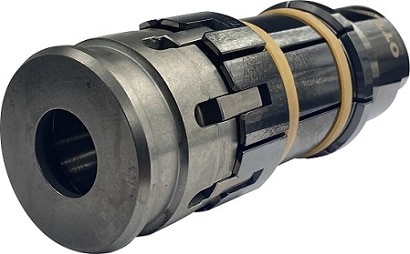
Aufnahmen für verschiedene Werkzeuge
Am Steil- bzw. Hohlschaftkegel lassen sich Werkzeuge mit Hilfe verschiedener Aufnahmen unterschiedlich gespannt werden. Die Werkzeuge sollten in den jeweiligen Bearbeitungszentren so gespannt sein, dass eine sehr gute Plan- und Rundlaufgenauigkeit sowie eine hohe Wiederholgenauigkeit in der Positionierung beim Werkzeugwechsel gewährleistet wird. Auch ist auf eine gute Biege- bzw. Verdrehsteifigkeit und auf die Möglichkeit hoher Umdrehungsfrequenzen zu achten. Zu den unterschiedlichen Aufnahmen zählen:- Spannzangenfutter
- Weldon-Aufnahmen
- Bohrfutter
- Schrumpffutter
- Hydrodehnspannfutter
Werkstück-Spanntechnik
Ein schnelles und präzises Spannen von Werkstücken ist für die Leistungsfähigkeit und die Performance der Zerspanung entscheidend. Denn damit sich eine Produktion langfristig rechnet, muss das Fertigungsverfahren effizient und wirtschaftlich sein. Hierbei kann die Werkstück-Spanntechnik einen wichtigen Beitrag leisten, indem sie eine sichere Verbindung zwischen Maschinentisch und Werkstück gewährleistet.Die verschiedenen Spannmittel
Welcher Halter für ein prozesssicheres Spannen des Werkstücks auf der Maschine am geeignetsten ist, hängt im Wesentlichen vom jeweiligen Bearbeitungsverfahren und der Form des zu bearbeitenden Bauteils ab. Im Folgenden werden die unterschiedlichen Spannmittel aufgezeigt:- Spannfutter: Kraft- bzw. Handspannfutter werden insbesondere auf Drehmaschinen eingesetzt. Es besteht aus einem Flansch, der die Maschinenspindel mit dem Futterkörper verbindet. Dieser umschließt und stabilisiert die Spannstelle. Ein sogenannter Zugrohradapter verbindet die Spannmittelkupplung mit dem Spannzylinder der Maschine und öffnet oder schließt das Spannsystem. Die Kupplung hält und bewegt den Spannkopf, welcher das Werkstück fixiert. Zur exakten Positionierung des Werkstücks wird ein Grundanschlag verwendet, dieser kann entfernt werden, um vollen Durchlass für die Stangenbearbeitung zu erhalten.
Die Spannfutter besitzen meist drei Spannbacken, für andere Geometrien oder dünnwandige Bauteile können auch vier, sechs oder mehr Backen verwendet werden. Die Spannbacken haben einen großen Einfluss auf die Spannqualität und die Spannsicherheit. Dabei wird zwischen harten und weichen Spannbackensätzen unterschieden. Harte Spannbacken sind verschleißfest, eignen sich für große Spannkräfte und besitzen verzahnte Spannflächen, welche allerdings die Oberfläche des Werkstücks beschädigen. Weiche Backen beschädigen die Oberfläche des Werkstücks nicht, besitzen eine hohe Wiederholspanngenauigkeit und können im Durchmesser sowie der Tiefe angepasst werden. Damit die Nutzung bei höheren Bearbeitungsdrehzahlen gewährleistet werden kann, ist das Spannfutter mit einem Fliehkraftausgleich ausgestattet. Dadurch können Spannkraftverluste ausgeglichen werden. Beim Beladen des Spannfutters wird das Werkstück in den Spannkopf geführt und durch den Grundanschlag positioniert. Der Spannkopf wird in den Konus gezogen und schließt sich um das Werkstück, wodurch dieses kraftvoll gegen den Grundanschlag gezogen wird. Die daraus resultierende steife Spannung reduziert Vibrationen während der Bearbeitung und stabilisiert das Werkstück.
- Spanndorn: Typischerweise wird der Spanndorn direkt auf einer Maschinenspindel befestigt und über eine keglige oder zylindrische Aufnahme zentriert. Somit werden beim Drehen die Drehbewegungen und -momente auf das eingespannte Werkstück weitergeleitet. Die Innenspannung erfolgt in einer Bohrung oder Innenkontur. Das haltende Element des Spanndorn ist die Segmentspannbüchse. Die Spannbüchse wird von einer Kupplung bewegt, welche wiederrum von einem Dornkörper gehalten wird, und wird von dem Spannmittel betätigt, auf dem der Spanndorn montiert ist. Die Kupplungsschale verbindet Spannbüchse und Kupplung. Auch beim Spanndorn positioniert und stabilisiert der Grundanschlag das Werkstück und schützt obendrein vor Verschmutzung im Spannsystem. Beim Beladen des Werkstücks wird die Spannbüchse auf den Konus gezogen und weitet sich, wodurch sie am gesamten Durchmesser Kontakt zum Werkstück hat und es gegen den Grundanschlag zieht. Dadurch wird das Werkstück stabilisiert und Vibrationen werden verringert.
- Spannzange: Im Gegensatz zum Spanndorn kommt die Spannzange bei der Außenspannung zum Einsatz. Sie ermöglicht ein genaues, schnelles und kraftschlüssiges Aufspannen. Die Spannzange besteht aus einer kegelförmigen radial geschlitzten Hülse mit einer runden, und manchmal auch quadratischen oder sechseckigen Bohrung. Dazu gehört eine Spannzangenaufnahme mit passendem Innenkegel. Die Spannung erfolgt mittels Überwurfmutter, mit der die Spannzange in den Innenkegel der Aufnahme gedrückt wird. Durch die Schlitzung wird die Bohrung im Spannmittel gleichmäßig zusammengedrückt, wodurch das Werkstück kraftschlüssig festgehalten wird.
Erfahren Sie mehr über unsere Produktpalette im Bereich der Werkzeug-Spanntechnik!
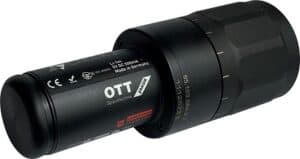
Einzugskraft-Messgeräte
Werkstück-Spanntechnik
Im Laufe der Entwicklung von Werkstückspannsystemen werden zwei Aspekte deutlich: Auf der einen Seite garantieren Schnellwechselsysteme und modulare Baukasten die immer wichtiger werdende Flexibilität und das schnelle Umrüsten der Spannmittel. Auf der anderen Seite werden im Zuge der Digitalisierung Sensoren in Spannsysteme integriert, die anschließend wichtige Daten zur Bearbeitung liefern. Gerade in der Serienfertigung setzen Zerspaner mehr und mehr auf intelligente Fertigungsstrukturen mit hohem Automatisierungs- und Digitalisierungsgrad.
Erfahren Sie mehr über unsere Produktpalette im Bereich der Werkstück-Spanntechnik

Abstützelemente

Hydraulikzylinder
