Linear technology
Startseite » Linear technology
What is linear technology?
Linear technology belongs to the technical sub-discipline of drive technology and deals with mechanical components or mechatronic systems for executing translational movements. The special feature of linear guides and drives is running with low friction and the ability to absorb transverse forces without noticeable deformation. In industry, linear technology is one of the most popular techniques when it comes to automation. This results not least from the robustness, reliability and ease of implementation of linear systems.
Linear units can also be easily combined with each other. This allows positioning in two or three directions. Complex processes can thus be implemented at comparatively low cost. The most important component of a linear unit is the linear guide, which determines the direction of movement. A linear guide consists of two components: the guide (=rail) and the transport element (=slide).
Linear systems are used in various technical systems. These include mechanical engineering (infeed and feed movements), building technology (sliding doors, sliding windows, ventilation flaps, skylights, etc.), handling systems (storage systems, placement) and rail vehicles with linear motors (Transrapid, certain subways or roller coasters).
Linear guides
Guideways can be differentiated according to the type of movements, the type of contact points and the principle of rolling element circulation. Movements on machines are only made possible by the guides. Depending on the type of guide, forces and torques can be transmitted in specific directions between moving and non-moving components. Guides are generally differentiated according to their respective type of motion.
What linear guides exist?
Linear guides, which are also referred to as guide systems, can be divided into sliding guides, rolling guides (ball guides, roller guides and track roller guides) and magnetic guides:
- Sliding guides:Sliding guides slide directly over a surface with low friction. Here, the contact area is significantly larger compared to ball or roller guides, which makes sliding guides more resilient, while friction increases at the same time. In this type of guide, a profiled sliding shoe slides along a likewise profiled rail and thus ensures that the carriage cannot leave its path. Compared to recirculating ball bearing guides, sliding guides have the advantage of being more economical in terms of price and thus represent a more cost-efficient solution. Also, their service life under constant, heavy load and their stability is often better.
- Rolling guides:Rolling guides generally include all linear guides in which rolling elements are used. Basically, these include rail guides (profiled rail guides, telescopic rail guides and cage rail guides) and shaft guides. Profiled rail guideways are a widely used linear guideway in mechanical engineering. In rolling guides, rolling elements roll between the carriage and the guideway on hardened raceways. The rolling elements form a circuit due to the recirculation in the carriage; this design enables endless guidance with unlimited stroke. The rolling elements used are balls (linear recirculating ball bearing and guideway assemblies or linear recirculating ball bearing and guideway assemblies), rollers (roller guideways or linear recirculating roller bearing and guideway assemblies) or track rollers with rolling bearings (track roller guideways). The principle of multiple point contact ensures lower friction than with sliding guides and optimally distributes the forces acting on the guide. Rolling guides can support high loads in a small space.
- Magnetic guides: In magnetic guides, the moving and stationary machine parts are separated by magnetic force. The moving machine part floats and thus the guide is contactless.
Our range includes various rolling and sliding guides. Please feel free to contact us and let us know your requirements. We will be happy to submit a non-binding offer and contact you to discuss the details. Please use our contact form or send us an email to info[at]pach-systems.de. Below you will find further information on roller guides / profiled rail guides and sliding guides.
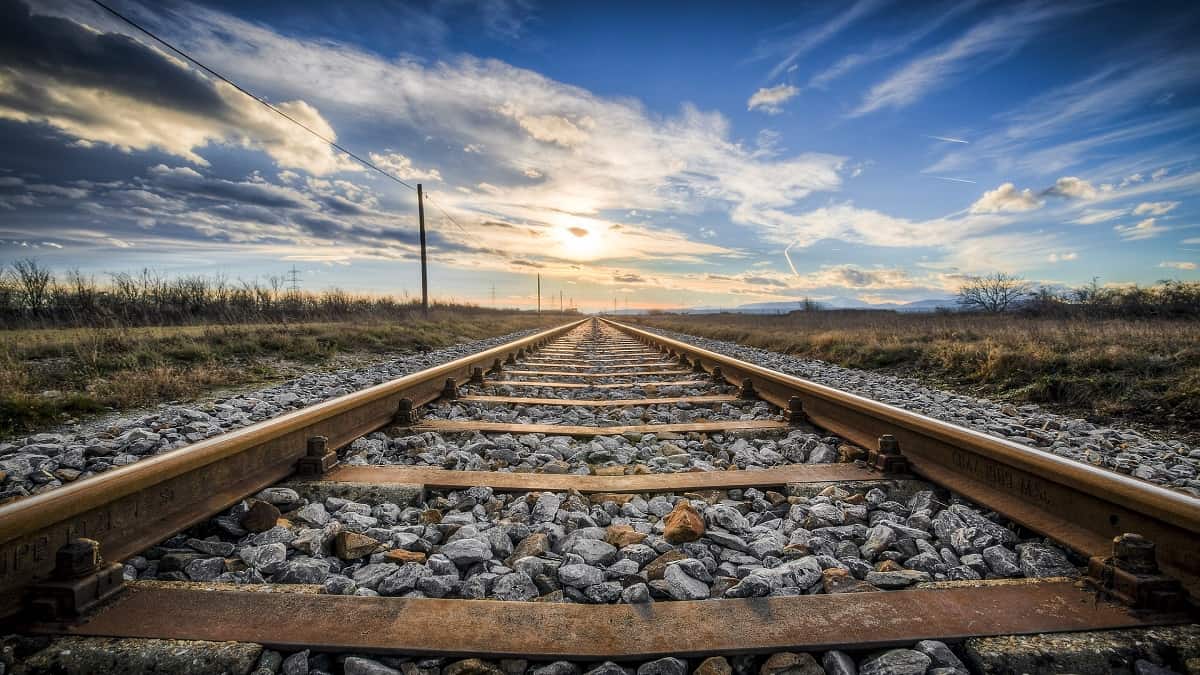
Rolling guides / Profiled rail guides
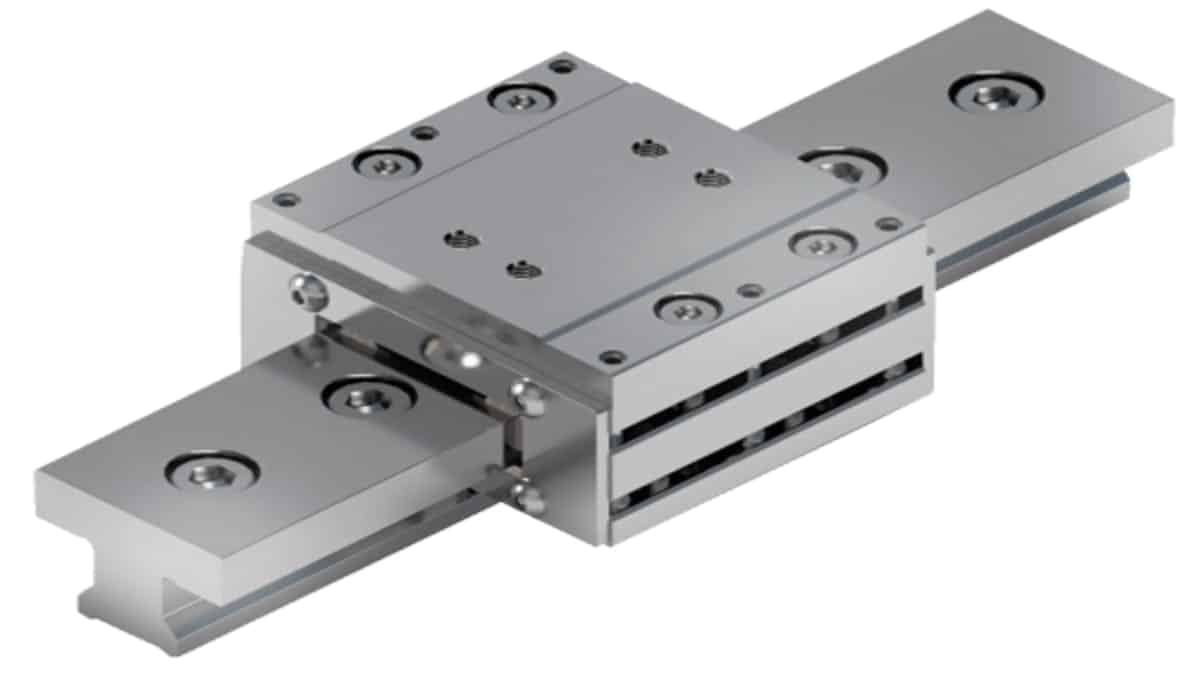
Sliding guides
Linear actuators
The choice of the right linear actuator is largely responsible for the overall performance of a linear unit. Linear actuators have a direct impact on the precision, speed, load capacity and cost of a solution.
The following linear actuators are common in practice:
- Ball screws
- Roller screws (Roller screw drive with roller recirculation and planetary roller screw drive)
- Timing belt drives
- Rack and pinion drives
- Chain drives
- Linear motors
- pneumatically or hydraulically operated synchronized cylinders
Information on the individual linear actuators can be found in the respective subchapter.