Dynamic Seals
Startseite » Sealing technology » Dynamic Seals
Dynamic seals have the task of sealing two components moving relative to each other in order to prevent a possible exchange of substances or to limit it to a permissible level.
Depending on the type of relative movement of the components to be sealed, a distinction is made between rotary and translational seals. Furthermore, dynamic seals can be divided into non-contact seals and contact seals. In the case of contact seals, the seal between the two components is compressed to such an extent that even microscopic gaps become so small that the substance to be retained can no longer penetrate. With non-contact seals, there is no mechanical contact between the two parts and the sealant. The sealing effect is achieved by contactless gaskets due to very narrow gaps. The non-contact nature results in a very long service life, but greater leakage losses must be accepted. Non-contact seals are often used when the surfaces to be sealed move at high speeds relative to each other, long service lives are desired, or maintenance is very difficult.
In the case of dynamic seals, the very widely varying operating limits must be taken into account. This refers primarily to the permissible sliding speeds. In addition to the permissible sliding speed, other conditions are decisive for the suitability of dynamic seals:
- Level of sealing performance
- Medium to be sealed (e.g. oil, water, chemicals, etc.)
- Size of pressure difference
- Temperature differences
- Translatory, rotatory movements or a combination of bot
- Degree of contamination
- Installation effort
- Maintenance and costs
We have the following dynamic seals in our assortment
Wipers
Wipers prevent dust and dirt particles from entering the interior of hydraulic and pneumatic cylinders when the piston rod is retracted. In doing so, they not only protect the sealing system from damage, but also the hydraulic fluid from contamination. This is achieved by a protruding wiper lip that retains the residual oil film on the piston rod. In addition to a protruding wiper lip, wipers acting on both sides have an inwardly directed sealing lip which prevents excessive lubricant film formation on the rod when the stroke is extended and allows the retained residual oil to be returned to the system via a leakage hole when the rod is retracted. Due to their function, wipers are an important part of the sealing system of hydraulic machines, because one of the main causes of damage, malfunction and downtime is contamination of the hydraulic fluid. Depending on the profile selection, wipers are used in a wide variety of applications and can be found, for example, in construction machinery, material handling vehicles or even presses.
Wipers are available in various materials (e.g. NBR, TPU and PTFE). NBR seals (acrylonitrile butadiene rubber) are particularly elastic and are suitable for use in smooth-running hydraulics. TPU (thermoplastic polyurethane) seals are most commonly used in modern hydraulic systems and have high wear and extrusion resistance. PTFE (polytetrafluoroethylene) seals have low coefficients of friction and very good wear properties, making them ideal for high sliding speeds.
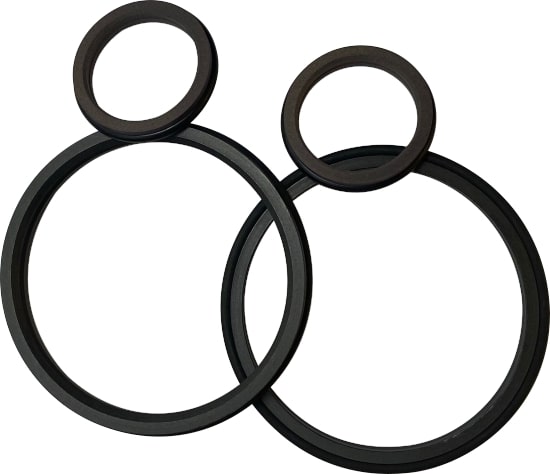
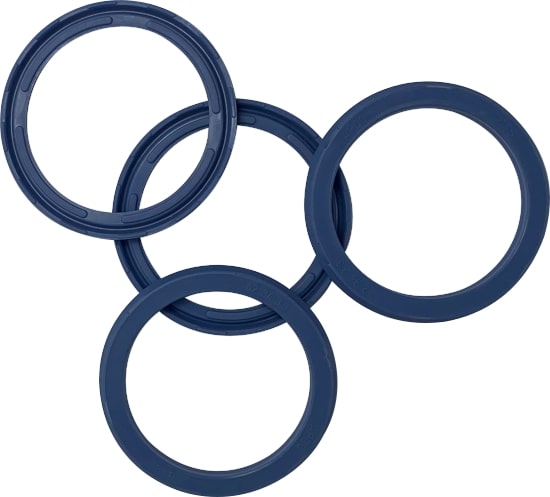
Piston seals
Piston seals are of crucial importance within the overall sealing system for the functionality of hydraulic cylinders. This seal is located in a groove on the outside of the piston. The purpose of the piston seal is to separate the two adjacent pressure chambers in the cylinder, maintaining pressure in one chamber so that it cannot escape into the other. Hydraulic cylinders frequently operate bidirectionally, which is why the piston seal often has to absorb the pressure from both sides. This requires double-acting piston seals that seal in both directions and can thus build up pressure on both sides of the piston.
Depending on the specific operating conditions, piston seals can also be preloaded by an O-ring or a metal spring. This results in a pre-pressure on the sealing surfaces, which can promote higher tightness, even without system pressure.
If piston seals are used in pneumatics, the changed requirements must be taken into account, since friction conditions (increased sliding friction) and the pressure medium are different. Specially adapted shapes and designs are therefore available for this area of application. They are also called pneumatic piston seals.
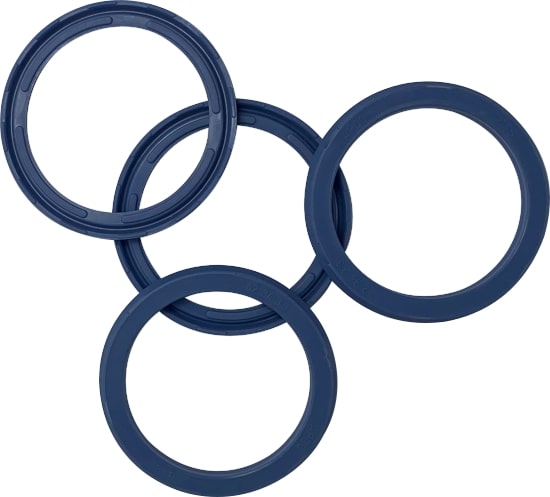
Rod seals
Rod seals have the task of sealing hydraulic cylinders on the rod side. These are internally sealing gaskets that are often designed as grooved rings, lip rings or compact rings. Rod seals are installed in the housing or a cylinder screw fitting and dynamically seal the sealing gap between the hydraulic cylinder and piston rod.
Rod seals have a different function than piston seals. Piston seals are installed in the piston itself. On the piston side, therefore, a static seal is achieved, whereas on the cylinder side a dynamic seal is achieved. Piston seals therefore seal with their outer diameter, which is also referred to as external sealing. In comparison, rod seals are installed in a fixed position in the cylinder housing and provide a static seal on the cylinder side. At the gap to the moving piston rods, they seal dynamically. Rod seals therefore seal with their inner diameter, which is also referred to as internal sealing.
Rod seals are available in various profiles and designs. The exact geometry influences the properties in terms of leakage rate, operating temperature, operating conditions and operating pressure (in combination with the material used for the rod seal). If a static seal with low friction and no system pressure is required, pre-stressed seals are used. In this case, a component acting as a preload element (e.g. O-ring) presses the seal lips apart and presses them against the sealing surfaces.
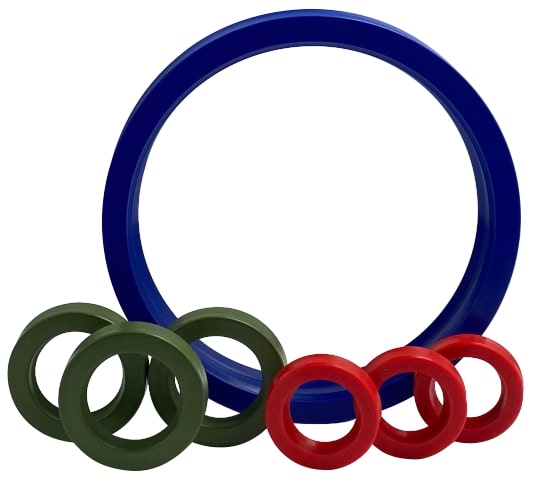
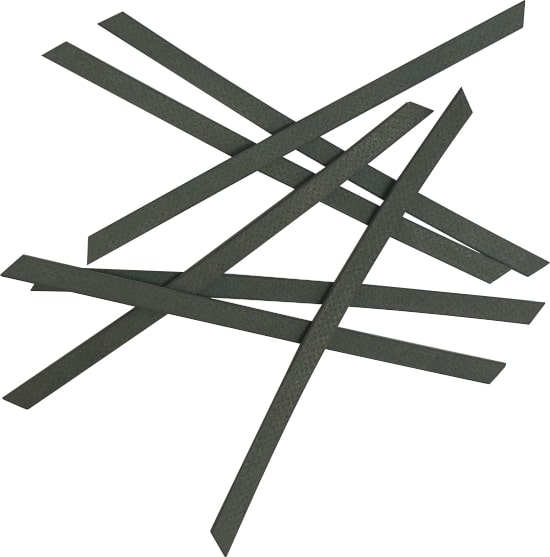
Rod and piston guide rings
Rod and piston guide rings are of enormous importance for the safe functioning of hydraulic or pneumatic systems and must be adapted to current conditions. The guide rings have the task of preventing metallic contact between the piston / rod and bore and safely absorbing all transverse forces that occur. The guide rings are manufactured in turned design with bevel cut from different materials.
The choice of the correct guide ring depends on various influencing variables. In addition to the pressure and the speed of movement, these also include the type of lubrication and the coefficient of friction. Guide rings that are subjected to high pressure should preferably be made of resistant material, e.g. fiber-reinforced plastics or steels. Steel guide rings require constant lubrication and are significantly heavier than plastic guide rings. The latter are often self-lubricating. Solid lubricants, such as added PTFE, help to ensure the lowest possible friction values and protect the piston rod or cylinder from wear.
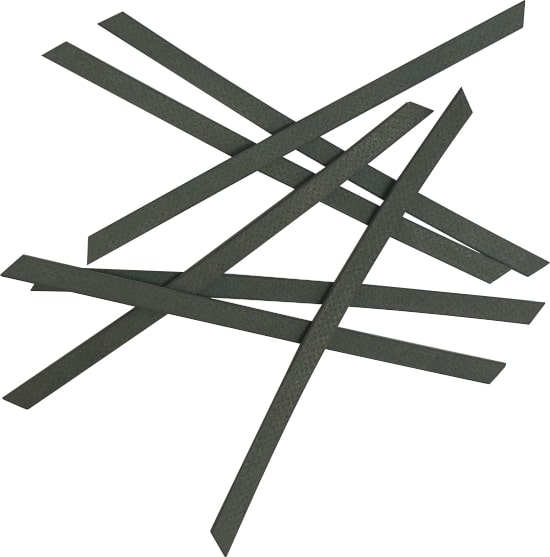
Rotary Shaft Seals
Rotary shaft seals belong to the lip seals and have the task of protecting the rotating shaft from contamination and sealing off lubricating oils and greases.
Radial shaft seals (abbreviation RWDR) are installed with a tight fit in the housing or housing cover, sealing the space between the shaft and housing at low pressure differences. Radial shaft seals consist of an elastomer part, a stiffening ring and a tension spring. Shaft seals can seal both when the shaft is stationary and when it is rotating. At shaft standstill, the sealing effect results from the radial contact pressure of the sealing lip on the shaft surface. The contact pressure is achieved by preloading and supported by the tension spring.
When the shaft is rotating, the sealing lip runs on the surface of the rotating shaft and is usually pressed radially onto the shaft by a hose spring. To reduce wear on the sealing lip, shafts are often ground to be twist-free in the area of the sealing surfaces. Some more modern types of shaft seals no longer have a hose spring (diaphragm shaft seals). Alternatively, these designs have a PTFE sealing lip.
If there are pressure differences between the two areas separated by the seal, the open side of the seal ring should face the area with the higher pressure. The pressure difference then presses the sealing lip against the shaft. Otherwise, the sealing lip can be pressed away from the shaft against the spring force, resulting in a loss of the sealing effect.
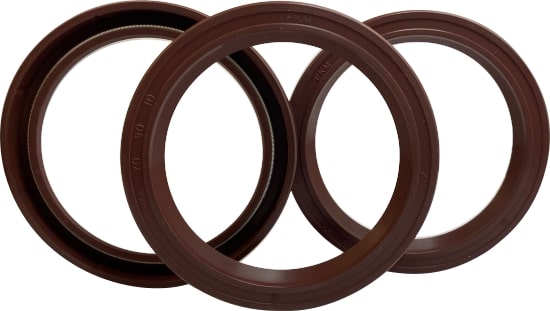
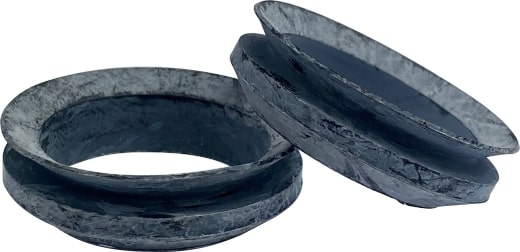
Axial shaft seals / V-rings
In contrast to rotary shaft seals, axial shaft seals do not seal on the shaft but on an axially directed housing part. The most common designs include the V-ring and the gamma ring. V-rings consist of an elastomer material, whereas gamma rings consist of two components, an elastomer material and a metal ring. The metal ring protects the rubber material.
Although V-rings are simple in design, they reliably seal against dirt, splash water and lubricants and protect the bearing position. Low frictional forces developed during operation are a major advantage. At high speeds, the sealing lip detaches from the shaft due to centrifugal force and the V-ring becomes a non-contact seal. As a result, the seal then functions as a spinning ring, which keeps loss values low and precludes wear of the sealing point.
Axial shaft seals are often used as secondary seals of rotary shaft seals when a high dirt load is to be expected.
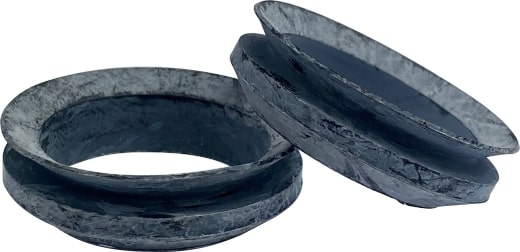
Nilos rings
Nilos rings are extremely robust and low-wear metal seals for extreme operating conditions on rolling bearings. This seal achieves its sealing effect by the sealing edge of the standard forms contacting the face of the rolling bearing ring to be sealed under slight pressure and grinding into the hardened rolling bearing ring. As a result of the grinding process, the Nillos ring changes over time from a contacting seal to a contact-free gap seal.
The proven sealing element is available in two basic types as standard:
- Nilos rings for sealing the outer rolling bearing ring AV.
- Nilos rings for sealing the inner rolling bearing ring JV
These two basic types represent the most frequently used designs. In addition, other designs are available that are suitable for sealing sealed rolling bearings and tapered roller bearings.
If angularly movable bearings (spherical roller bearings, self-aligning ball bearings) are used in designs to compensate for angular errors, Nilos rings are unsuitable for sealing.
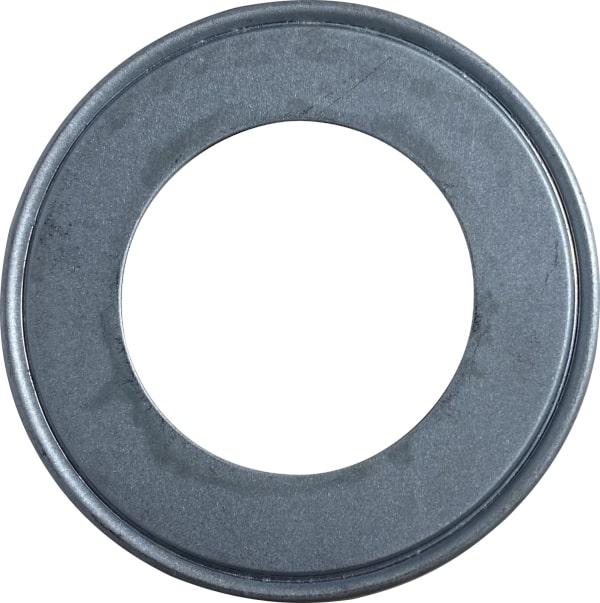
PACH Systems offers you a wide product range of different dynamic seals. For this purpose we cooperate with our long-term partners. Please let us know your requirements via our contact form. We will be happy to provide you with a non-binding offer or contact you to discuss the details.