Rolling bearings
Startseite » Rolling bearings
Rolling bearings are one of the most prevalent and important components in machine manufacturing. Rolling bearings are bearings that facilitate the movement of components by means of a rolling motion and significantly reduce friction. In contrast to plain bearings, the friction loss is at least ten times lower. Rolling bearings are particularly suitable for high speeds with reduced noise and heat generation. Rolling bearings are therefore used in particular for the location of axles and shafts that are to implement rotating movements. Lubricants can further optimize the processes here.
The structure of rolling bearings
Rolling bearings are normally of the same design, but differ mainly in the arrangement and shape of the rolling elements used. Almost all rolling bearings consist of an inner and outer ring, between which the rolling elements are located that roll in the raceways. A cage is usually used to ensure uniform distribution and guidance of the rolling elements. The rolling elements of the bearings (balls or rollers/needles) are also used for differentiation, so that a distinction is made between ball and roller bearings.
The key difference: point or line contact
The key difference between the two designs lies in the contact between the rolling elements and the raceway surface. Whereas in the case of ball bearings the contact between balls and raceway surface is point-shaped from a geometrical point of view, the rolling elements of roller bearings contact the raceway surface in a linear manner. Both types of contact have their advantages and disadvantages. Point contact favors the operation of ball bearings at high speeds, although they cannot support as high loads as roller bearings. Roller bearings, on the other hand, have a larger contact area, which means they can support heavier loads and have greater rigidity. Conversely, the frictional torque of roller bearings is greater than that of ball bearings, which means that they are used in particular in applications with comparatively low speeds (e.g. in gearboxes).
More detailed information on the individual ball bearing and roller bearing types can be found under the respective sub-pages. The following table provides a rough overview.
Bearing | Picture | Advantages | |
---|---|---|---|
Ball bearings | |||
![]() |
| ||
![]() |
| ||
![]() |
| ||
| |||
Roller bearings | |||
![]() |
| ||
![]() |
| ||
![]() |
| ||
![]() |
|
Various factors are important when selecting the right rolling element and bearing. The right choice depends, for example, on the speed, load and type of load (axial or radial).
Materials of rolling bearings
The inner and outer rings, as well as the rolling elements, are generally made of high-purity chrome-alloyed special steel. This material not only offers the required hardness and purity, but also fulfills the important requirements of high load carrying capacity and long service life. In addition to chrome-alloyed special steel, special materials such as ceramics and plastics are also used. Although plastics cannot withstand extremely high temperatures, they are significantly lighter than steel. The cages of the rolling bearings are mainly made of steel, brass and plastic. However, special designs are also possible here.
For special operating conditions and fields of application, rolling bearings are also available in special designs, ranging from stainless steel to hybrid bearings in which, for example, the bearing rings are made of steel and the rolling elements are made of ceramic. Hybrid bearings can be used, for example, in spindle bearings for machine tools.
Cover plates / Sealing washers
Rolling bearings without cover plates or sealing washers are not protected against dirt or foreign bodies from the outside. As a rule, these types are used in closed installation situations, e.g. in closed gearboxes. As an alternative to the open design, rolling bearings are also offered by many manufacturers with sealing washers or cover washers on both sides or on one side. Sealing washers or cover washers retain the grease required for lubrication in the bearing.
The structure of rolling bearings
Rolling bearings are normally of the same design, but differ mainly in the arrangement and shape of the rolling elements used. Almost all rolling bearings consist of an inner and outer ring, between which the rolling elements are located that roll in the raceways. A cage is usually used to ensure uniform distribution and guidance of the rolling elements. The rolling elements of the bearings can have different shapes and are also the eponym for the different types of rolling bearings.
Ball = Ball bearing (deep groove ball bearings, angular contact ball bearings, self-aligning ball bearings, radial insert ball bearings)
Needle = needle roller bearings
Cylinder = cylindrical roller bearings
Barrel = Barrel or spherical roller bearing
Taper = Tapered roller bearing
Various factors are important when choosing the right rolling element. The right choice depends, for example, on the speed, load capacity and type of load (axial or radial).
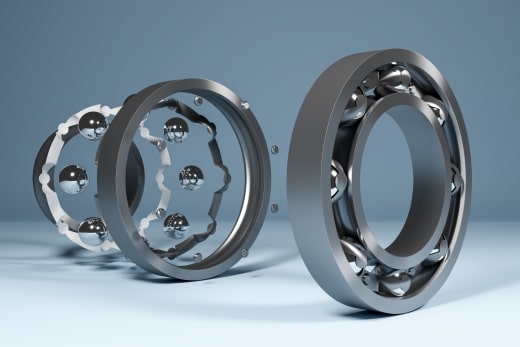
Materials of rolling bearings
The inner and outer rings, as well as the rolling elements, are generally made of high-purity chrome-alloyed special steel. This material not only offers the required hardness and purity, but also fulfills the important requirements of high load carrying capacity and long service life. In addition to chrome-alloyed special steel, special materials such as ceramics and plastics are also used. Although plastics cannot withstand extremely high temperatures, they are significantly lighter than steel. The cages of the rolling bearings are mainly made of steel, brass and plastic. However, special designs are also possible here.
For special operating conditions and fields of application, rolling bearings are also available in special designs, ranging from stainless steel to hybrid bearings in which, for example, the bearing rings are made of steel and the rolling elements are made of ceramic. Hybrid bearings can be used, for example, in spindle bearings for machine tools.
Lubrication of rolling bearings
The lubrication of rolling bearings is an important topic and is essential for the reliable working of rolling bearings. Statistically, around 80% of all rolling bearing failures are due to lubrication. It is therefore important to pay particular attention to correct lubrication. Lubrication fulfills the following tasks:
Creating a load-bearing lubricant film between the rolling element and the inner or outer ring.
Protecting the rolling bearing from corrosion
Damping the running noise
Protecting the rolling bearing from contamination (grease lubrication)
To dissipate heat (oil lubrication)
Greases, oils or solid lubricants (special cases) can be used to lubricate rolling bearings. The choice of lubricant to be used depends largely on the level of stress, speed and operating temperature of the bearing.
Grease lubrication
Grease lubrication requires low maintenance and usually provides sufficient protection against contamination, which makes it possible to seal bearings easily and cheaply.
Calcium, sodium, aluminum and lithium soap greases are usually used to lubricate rolling bearings. The type of grease to be used depends on the operating temperature, behavior against moisture, sealing behavior and consistency. Calcium and lithium greases are mostly used to lubricate highly loaded bearings. Lithium soap grease with silicone oil has better temperature properties but lower load capacity.
The natural aging and contamination of the grease requires renewal at certain intervals (lubrication interval). If the lubrication period is longer than the service life of the rolling bearing, permanent lubrication is used. Permanent lubrication means that the bearing receives a single grease filling (e.g. in the case of deep groove ball bearings with cover or sealing washers).
Oil lubrication
Oil lubrication is used when high speeds or medium speeds at higher loads or the operating temperature no longer permit grease lubrication or when the oil is used for heat dissipation or where adjacent components are already oil-lubricated.
The type of oil to be selected depends on the requirements of the components without any disadvantages for the rolling bearings. Mineral-based oils which meet the minimum requirements according to DIN 51501 are suitable for lubricating the rolling bearings; however, oils with better aging resistance according to DIN 51517 are preferable.
We offer the following types of products